ご案内
2024.05.10
【3Dプリンティング/AM用語集】
この用語集は、一般社団法人日本3Dプリンティング産業技術協会様と当協会が共同で作成しました。
①AM用語
N0. | 用語 | 説明 |
1 | 3DCAD/3DCAM | 3DCADは、PC上の仮想空間に3軸からなる立体形状(3Dモデル)を制作できるソフトウェアである。3DCADで設計またはデザインした3Dモデルデータを3DCAMソフトに転送してプリンター用データに変換し、さらに3Dプリンタに転送することで造形が可能になる。3DCAMでは、3Dモデルデータのの断面のデータ(スライスデータ)を計算し、スライスデータからツールパスと呼ばれる3Dプリンタの機構を直接駆動するデータ(G-code)を計算する。3DCADから3DCAMに転送する3Dモデルデータとして、STL形式のデータが用いられる。 |
2 | 3Dスキャナー | 対象となる物体の3Dデータを取得する機器。点群データで取り込み面データを生成して3DCADに取り込む。主にリバースエンジニアリングに利用する。表面形状を計測できる光学方式以外に、内部構造まで計測できるX線CTスキャナやMRI式のスキャナもある。 |
3 | 3Dプリンター | 通常の紙に平面(二次元)的に印刷するプリンターに対して、3DCAD、3DCGデータを元に立体(3次元のオブジェクト:製品)を造形する機器。3Dプリンターの造形方式 はJIS、ISOにて、以下の7種類に分類されている。 ①液槽光重合法 /VPP( Vat PhotoPolymerization) ②材料噴射法 / MJT(Material Jetting) ③結合材噴射法 / BJT(Binder jetting) ④粉末床溶融結合法 / PBF(Powder Bed Fusion) ⑤材料押出法 /MEX( Material Extrusion) ⑥指向性エネルギー堆積法 / DED(Directed Energy Deposition) ⑦シート積層法 /SHL( Sheet Lamination) |
4 | アディティブ・マニュファクチャリング(AM:Additive Manufacturing) | 材料を結合して立体物を造形する製造方法。正式な名称としてISOで定義されている。日本語での正式名称は「付加製造」(JIS)である。多くの場合は、造形層を積み重ねる形式なので、「積層造形」と呼ばれることもある。国内では、3Dプリンターを同義語として用いることが多いが、本来は個人用途含む非工業的な用途に用いられるものを指している。 |
5 | ラピッドツーリング(Rapid Tooling) | ラピッドプロトタイピングと同様に、射出成形や鋳造に用いる型や治具などを短期間でつくることをラピッドツーリングと呼ぶ。鋳型の製造コストを抑えられるのはもちろん、必要な時に必要なものをすぐに出力できるため、治具などをストックしておかなくて良いというメリットもある。 |
6 | ラピッドプロトタイピング(Rapid Prototyping) | デザインや形状などを確認するため、試作品を文字通り短期間(Rapid)で製作すること。3Dプリンターの普及にともない、これまで数日から数週間を要していた試作品の製造が大幅に短縮できるようになり、コストの削減につながっている。 |
7 | ラピッドマニュファクチャリング(Rapid Manufacturing) | 3Dプリンターを用いて、最終製品を製造すること。型などをつくらずに、最終製品を製造できるので、開発から市場に出るまでのスピードを大幅に短縮できる。1回につくれる量に限りがある3Dプリンターの性質から大量生産には向かないが、受注生産品などの少量の製品をつくる際には大きなアドバンテージとなる。デジタルデータから製品を作ることから、Direct Digital Manufacturing(DDM)という呼び方もある。 |
8 | STL形式 | STL:Standard Triangulated Languageの略。3次元データのファイル形式のひとつで、3Dプリンターでの標準データ形式。3D CADソフトウェアや3D CGソフトで作成したデータをSTL形式に変換することで、3Dプリンターでの造形に最適なデータへと変換できる。CADデータは高精度な曲面データが用いられるが、曲面データを三角形の集まりにより近似したものになる。複雑な形状ではSTLデータは非常に容量が大きくなり処理時間がかかる。そのため、近年は関数で表現することで軽量にした3Dモデル(Implicit Model)も登場している。 |
9 | 造形エリア | 3Dプリンターで造形ができるエリアのこと。縦・横・高さ(x.y.h)をmm単位等で表現する。円筒形の造形エリアを持つ機種の場合は、直径と高さ(d.h)で表現する。 |
10 | 造形サイズ | 3Dプリンターで造形できる造形物の大きさ。縦・横・高さ(x.y.h)をmm単位等で表現する。最大造形サイズ・形状は機種によって異なる。一般には造形エリアより小さくなる。 |
11 | モデル材 | 3Dプリンターで造形する際に造形物になる材料のこと。造形方式によりさまざまな種類のモデル材があり、造形物の使用目的に合わせて選ぶ必要がある。 |
12 | サポート材 | モデル材を支えて形状を保持するためのもの。3Dプリンターは、空中に浮いた部分を造形できないため、その空間を埋めるためにサポート材を使用する。樹脂成形の金型と同じ役割を担う。造形後は、サポート材を除去する必要があり、サポート材の使い方で造形モデルの品質、サポート材の除去のしやすさが変わってくる。水や薬品に溶解する比較的除去が容易な材料もある。 |
13 | 積層ピッチ | 造形時の一層あたりの厚み。数値が小さいほどより微細な造形が可能になる。ただし細かく積層するほど造形にかかる時間は長くなる。また造形精度は、その他のさまざまな条件も関わるため、一概に積層ピッチ=精度とは言えない。 |
14 | DPI | Dots Per Inchの略で、1インチの中にどれだけのドットを表現できるかを表す。3Dプリンターインクジェット方式のDPIはインクを噴射する間隔を表している。 |
15 | 後加工 | 研磨加工など3Dプリントした造形物に対し、より完成度をあげるために加工を施す作業。サポート材の除去から、表面の積層跡を無くして滑らかにしたり、液体レジンの洗浄といった基本的な作業や、切削、研磨など二次硬化して精度、強度と耐久性を高めたり、塗装を施したり、コーディング材の塗布なども行う。 |
16 | 切削加工 | 造形物の表面を磨いて滑らかにする処理。3Dプリンターは材料を積層して造形する特徴から、表面に積層の段差ができてしまうが、研磨することでその段差が目立たない滑らかな表面に仕上げることができる。研磨方式としては、バフ研磨、バレル研磨、電解研磨などがある。 |
17 | 研磨加工 | 造形物の表面を磨いて滑らかにする処理。3Dプリンターは材料を積層して造形する特徴から、表面に積層の段差ができてしまうが、研磨することでその段差が目立たない滑らかな表面に仕上げることができる。研磨方式としては、バフ研磨、バレル研磨、電解研磨などがある。 |
18 | 鋳造 | 主に鉄、アルミ、銅、真鍮などの金属を融解状態にして、型に流し込み成形する加工法。鋳造に用いられる型を、鋳型と呼ぶ。近年では、3Dプリンターで複雑な砂型を造形し、鋳型に用いることもある。 |
19 | ロストワックス | インベストメント鋳造方式の一つで、ロウでつくった原型を砂や石膏など台材に仕込んで、ロウを溶かして焼き固めて鋳型をつくり、それに金属を流し込み、製品を製造する。宝飾製品の製造に用いられることが多い。 |
20 | フィラメント | MEX方式(FDM方式)の3Dプリンターでの出力に使われる直径1.2mm程度の細長い樹脂。リールに巻き取った状態で提供されることが多い。2次元のプリンターでのインクに相当する。 |
21 | エクストルーダー | MEX方式(FDM方式)の3Dプリンターで、樹脂材料(フィラメントやペレット)を熱で溶かして、プリントヘッドへ送り込む機構のこと。 |
22 | ノズル | MEX方式(FDM方式)の3Dプリンターで、樹脂材料等が出てくる部分。ノズルを使い分けることによって造形品質や速度を切り替えることができる。 |
23 | ビルドプレート | 3Dプリンターの出力物が付着する基台のこと。 メーカー、造形方式によってプラットフォームの形や場所が異なる。 |
24 | キャリブレーション | 装置の動作を安定させるための、調整全般を指す用語。一例として、MEX方式(FDM方式)のプラットフォームの角度・位置調整が挙げられる。 |
25 | シールドガス | 金属3Dプリンターにて造形中の溶融金属の酸化、窒化などを防ぐため、大気を遮断するために使用されるものがシールドガスである。シールドガスとして使用されているのは、高温でも金属と反応しない化学的に安定したアルゴン、ヘリウムなどの不活性ガスがある。 |
26 | クラッディング | 日本語では「肉盛り加工」「皮膜加工」という意味になる。粉末やワイヤーをレーザー光の熱で瞬時に融解し、母材表面に堆積させることで、同種または異種の金属を溶接する。異種材を肉盛りすることで母材の特性を向上させたり、擦り減った部分の補修になどに利用される技術。3Dプリント技術分類ではDED方式に分類される。 |
27 | DfAM(ディーファム) | 「Design for Additive Manufacturing(付加製造のための設計)」の頭文字を取った略称。DfAMはAMのメリットを最大限に活かすための設計ガイドラインでありツールであると言える。またAMのデメリットと考えられるサポート除去工程などについて、サポートが極力不要となるような形状を設計し、デメリットを解消する考え方も含む。 |
28 | ジェネレーティブデザイン | 設計の目的や条件をコンピューターに与え、数百~数千個の設計を自動生成させる手法。大きな特徴として、設計者が作成したプロトタイプを必要としないことが挙げられる。設計の条件をもとに、コンピューターがゼロから設計を行うことが可能となる。ジェネレーティブデザインの結果には、オーソドックスなものから思いもよらないものまで、幅広い設計が含まれる。 |
29 | トポロジー最適化 | 与えられた設計条件を元に、シミュレーションを繰り返して3Dモデルの形状や構造(穴や中空、トラス等)の最適値を自動的に求めていく手法である。最初に与える設計条件は、設計領域や荷重がかかる場所や荷重の量などを指定する。 |
30 | 中空構造 | 中が空洞になっている構造で、従来構造に比べて、軽量化や低コストのメリットがある。3Dプリンターでは、中空構造のモデルを直接作る事が可能である。 |
31 | ラティス構造 | 軽量化と強度を両立させるための、多孔質な3Dモデルのデザインパターン。軽量化することで、材料の節約によりコストダウンも達成している。同じパターンの繰り返しで表現されることが多かったが、ジェネレーティブデザインを用いて生成したパターンが徐々に変化していくものが主流になっている。 |
②造形方式
N0. | 造形方式 | 説明 |
1 | 液槽光重合方式 / VPP(Vat PhotoPolymerization) | 一般的には「光造形」や「SLA (Stereolithography)」と呼ばれる方式。タンクに貯めた液体の光硬化性樹脂にレーザーなどを照射することで必要な部分を1層ずつ硬化させ、積層させる造形法。光を照射する向き(上面 / 下面)と照射する方法(レーザー / プロジェクター)の違いで分類できる。断面に光を当てる方法としては、レーザをガルバノミラー等で走査する方法、またはプロジェクタを使用して断面形状を一括で露光する方法がある。後者には、「DLP(Digital Light Processing)」、LCD(Liquid Crystal Display)などがある。 |
2 | 材料噴射法 /MJT( Material Jetting) | 一般的には「インクジェット式」と呼ばれる方式。3Dプリンターのノズルからモデル材とサポート材をステージに噴射し、一層積層するごとに造形ベッドが下がり次の層を積層する。材料に応じて紫外線の照射や加熱、冷却することで硬化させ、複雑な造形物を高解像度、高精度にモデリングできる造形方式。また、複数のモデル材を混ぜ合わせることが可能なため、カラー表現や異なる材料を混合して新たな物性を得ることも可能。材料噴射法は、使用する材料や材料を噴射するノズルの違いにより、MJ(Material Jetting:主に光硬化性樹脂)、NPJ(Nano Particle Jetting:金属、セラミックス等)、DOD(Drop on Demand:ワックス)などに分類される。 |
3 | 結合材噴射方式 / BJT(Binder jetting) | 粉末状のモデル材にバインダーとよばれる結合剤をノズルから固化させたい場所にのみ噴射し、熱反応や化学反応を利用して固める造形法。モデル材には樹脂や金属、砂や石膏が用いられ、樹脂や石膏の場合にはバインダーを着色することで、フルカラーの造形ができる。造形後に焼結や含浸処理が必要な場合がある。通常、サポート不要で造型が可能な方式である。 |
4 | 粉末床溶融結合方式 / PBF(Powder Bed Fusion) | 一般的には「粉末焼結」や「SLS(Selective Laser Sintering)」「SLM(Selective Laser Melting)」「EBM(Electron Beam Melting)」「HSS(High Speed Sintering)」と呼ばれる方式。SLS、SLM、EBMでは、平らに敷き詰めた金属、セラミックス、樹脂などの粉末にレーザや電子ビームを照射してモデルの断面形状に溶融結合させる。一層積層するごとに造形ベッドが下がり次の層を積層する。基本的には単一の材料を使った造形となる。セラミックスは溶融しないので、表面に樹脂などのコーティングが必要である。HSSでは、平らに敷き詰めた樹脂に、インクジェット方式で熱吸収材を断面形状に塗布した後、赤外線ランプなどを照射し、吸収した熱により材料を溶融結合させる。通常、樹脂粉末であればサポート不要であるが、金属の場合にはサポートが必要になることが多い。 |
5 | 材料押出方式 / MEX(Material Extrusion) | 3Dプリンタの中で最も多く使われている造形法であり、さまざまな物性の樹脂に幅広く対応している。一般的には「熱溶解積層法」「FDM(Fused Deposition Modeling)」と呼ばれることが多く、「FFF」も同様の意味で使われる。樹脂のフィラメントやペレットを溶融してノズルから押し出し、造形物の断面輪郭に沿って移動しながら積層することによりモデルを作成する。材料は主にABSやASA、PC、PEEK、ULTEMなどの熱可塑性の樹脂が用いられ、これらの材料を吐出ノズルの手前に設置したヒーターにより溶融する。ハイエンドの機種では、造形領域内の温度管理が高温に対応している機種も多いことから、さまざまな物性の樹脂に対応しており、エンジニアリングプラスチックやスーパーエンジニアリングプラスチックを使用することも可能。高強度のPEEKやPEIなどを活用することで、試作品だけでなく高性能な最終製品を造形できるようになってきた。さらに、溶融した樹脂と一緒にカーボンファイバーなどの繊維を同時に造形物内に設置して、強度の高い造形物を得る方式もある。また、主に建築用途としてコンクリートをノズルから押し出して積層する技術が登場している。この場合はコンクリートのスラリーを常温で押し出すのみで、加熱は行わない。 |
6 | 指向性エネルギー堆積方式 /DED( Directed Energy Deposition) | 「レーザデポジション」や「LMD(Laser Metal Deposition)」「DMP(Direct Metal Deposition)」と呼ばれることもある。レーザ、電子ビーム、プラズマアークなどの指向エネルギービームで金属粉末やワイヤー状の金属を溶融し、肉盛溶接する方式。レーザークラッディングは、この方式を応用した例である。Laser DEDは、金属粉末を吹きつけるのと同時にレーザを照射してモデルの輪郭形状に溶融・凝固させながら積層することでモデルの形状に固形化する。また、材料に金属ワイヤーを用い、ワイヤー先端に電圧をかけてアーク放電を起こしてそのエネルギーで金属を溶融、肉盛りするWAAM(Wire Arc Additive Manufactruing)方式、金属粉末を超音速で対象物に衝突させてそのエネルギーで積層していくColdSpray方式なども用いられている。 |
7 | シート積層方式 / SHL(Sheet Lamination) | シート材をモデルの断面形状に切断し、各層を接着、溶接しながら積層してモデルを作成する方式。材料は金属、樹脂、紙などで、フルカラーの立体モデルや複数の材料が混在したモデルを造形することも可能。 |
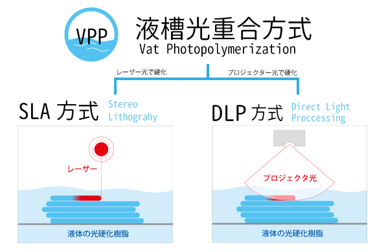
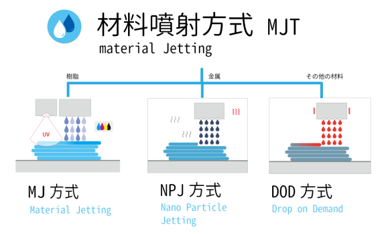
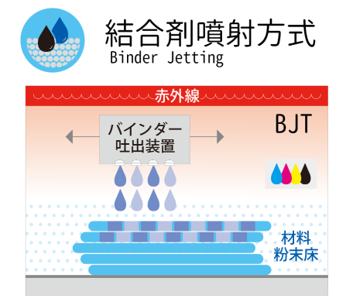


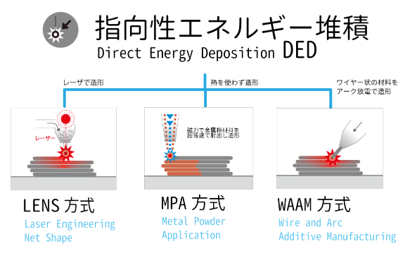
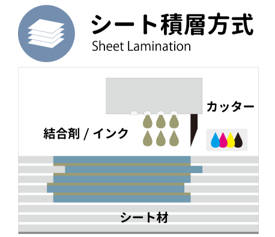
造形方式図 出典:ShareLab
③樹脂材料
No. | 材料 | 説明 |
1 | 熱可塑性樹脂 | 加熱すると軟化し、冷却すると硬化する樹脂。また加熱すると再び柔らかくなる。汎用プラスチック、エンジニアリングプラスチック、スーパーエンジニアリングプラスチックなどに分類される。 |
2 | 熱硬化性樹脂 | 熱硬化性樹脂は熱可塑性樹脂と異なり、加熱すると固くなる樹脂。一度固まると加熱しても柔らかくならない。 |
3 | エンジニアリングプラスティック | 強度と耐熱性に優れたプラスチックの総称。 数値上だと一般的には、耐熱性が100℃以上あり、強度が49MPa(500kgf/㎠)以上、曲げ弾性率が2.4GPa(24500kgf/㎠)以上を持つ高機能樹脂を指す。エンジニアリングプラスチック(エンプラ)の中でも特に高性能なものは「スーパーエンプラ」と呼ばれており、高い機能を必要とする工業部品などに用いられる。 |
4 | ABS樹脂 | アクリロニトリル (Acrylonitrile)、ブタジエン (Butadiene)、スチレン (Styrene)共重合合成樹脂の総称。CAS番号9003-56-9。ABSは原料の頭文字に由来する。常用耐熱温度は70~100℃。耐衝撃性・剛性などに優れていて、塗装後の加工がしやすいのが特長。電化製品の外装部品や事務機器のボディーなどに用いられることが多い。熱可塑性があり、主にMEX方式の造形材料として使われる。 |
5 | PLA樹脂 | ポリ乳酸(polylactic acid、polylactide)が重合した樹脂。イモ類やトウモロコシなどのデンプンからつくられる植物由来のプラスチックで、熱可塑性があるため、MEX造形の材料として用いられる。高温に弱く固いため、やすりがけなどで加工しづらく塗料がなじみにくいというデメリットもあるが、材料が粘り強く固く吐出後の収縮が少ないため大型の造形物に向いている。 |
6 | 光硬化性樹脂 | 紫外線など特定の波長の光によって硬化する樹脂。樹脂の分子が光により重合することによって分子量が増え、液体から個体に変化する性質を利用して、光造形方式やマテリアルジェッティング方式の3Dプリンターの素材として用いられる。UV硬化樹脂、紫外線硬化樹脂とも呼ばれる。光硬化するアクリル系材料を主成分とするが、分子構造の工夫や熱重合性成分との複合化により、硬化物の物性を既存の樹脂に近いものにすることが可能で、ABSライク、ゴムライク、PP(ポリプロピレン)ライク といった呼び方をする場合もある。硬化前の材料は皮膚感作性があることが多く、素手での取り扱いは注意を要する。 |
7 | アクリル樹脂 | 高い透明性を有する非晶質の合成樹脂で、透明性の高さから、水槽やレンズなどの材料としても用いられる。重合前のモノマーやオリゴマーは光硬化型3Dプリンター用材料の主成分として利用される。 |
8 | ABSライク樹脂(光硬化性樹脂) | 液状の材料に紫外線などを照射して硬化させる光造形法で用いられる素材となる樹脂の1種。造形物の物性はABSに似た特性を持つため、この名称で呼ばれる。本来のABSに比べると強度は劣るが、表面が滑らかで微細な造形物をつくることができるため、組付け確認や注型マスターなどの用途で使用されることが多い。 |
9 | PP(ポリプロピレン)ライク (光硬化性樹脂) | 液状の材料に紫外線などを照射することで硬化する光造形法で使用される。造形物の物性は、高い強度と柔軟性を有するポリプロピレンに似た特性を持つため、この名称で呼ばれる。 |
10 | ゴムライク(光硬化性樹脂) | 液状の材料に紫外線などを照射することで硬化する光造形法で使用される。硬化物はゴムのように柔軟性・弾性を持ち、ゴム製品の試作を製造するのに適しているため、この名称で呼ばれる。成分の調製により造形後の硬さを調整できるプリンターもある。 |
11 | ナイロン(PA・ポリアミド) | ポリアミド合成樹脂。「ナイロン」の名称は、1935年にナイロン6,6(6,6-ナイロンなど)の合成に成功したアメリカのデュポン社の商品ブランド名であるが商標ではなく一般名称として通用している。結晶性があり、PBF造形に適した熱特性を持つため、主にPBF樹脂造形用材料として用いられる。3Dプリント材料としては、PA(ポリアミド)という名称で表すことも多く、広く使われているPA12の他、PA11、PA6などがある。造形物は強度、靭性などナイロンの特性を持ち、実用品として活用されることもある。 |
12 | ポリカーボネート | 熱可塑性樹脂の一種。透明性や耐熱性、耐衝撃性などに優れており、航空機や輸送機器、電子光学、医療機器などの材料にも使用されている。耐熱性があり、エンジニアリングプラスチックに分類される。色材を混合することで着色も可能。MEX方式の3Dプリンター用の造形材料として用いられる。 |
13 | TPU(Thirmoplastic Polyurethane) | 熱可塑性樹脂の一種。ゴムのような伸縮性を持ち、強度、耐摩耗性に優れており、水蒸気透過性も持つ。3DプリンターではPBF方式やMEX方式での造形材料として活用されている。 |
14 | ポリプロピレン | 熱可塑性樹脂の一種。軽く、成型がしやすく、高い耐摩耗性、傷つきにくさ、耐薬品性などの特長から多くの産業で活用されている。3Dプリンター用としてはMEX造形用のフィラメントやPBF造形用のパウダーが供給されている。 |
15 | 生分解性樹脂 | 材料が自然界に存在する微生物などの働きで分解され、最終的には水と二酸化炭素として自然界に循環していく性質をもったプラスチック。植物性原料から作られるものと石油原料から作られるものがある。3Dプリンター用としても、サステナブルな材料として提供が始まっている。 |
16 | バイオ系素材 | 植物や動物、微生物などの生物に由来する原料を主原料とする材料。3Dプリンター用としては、ひまし油を原料としたポリアミド材料などが開発されている。 |
④金属材料
No. | 金属材料 | 説明 |
1 | 金属造形材料(全般) | 金属造形には様々な方式があり、材料としては大きく分けて以下の3種類がある。金属粉末、金属ワイヤー、金属粉末を含む樹脂。金属造形用粉末は、主にガスアトマイズ法、ディスクアトマイズ法、プラズマアトマイズ法の粉末が用いられている。また造形物の精度や密度を高め、かつ安定的に造形するために、粉末の形状や内部の状態、流動性、均質性、低酸素などの特性が求められている。3Dプリンター用の金属粉末の主な材料として鉄系(マルエージング鋼、ステンレスなど)、ニッケル系(インコネル)、チタン系、アルミニウム系、銅系、コバルトクロム系などの材料が用いられる。 |
2 | ガスアトマイズ法 | 金属粉末の製粉プロセスの一つ。溶融した金属に不活性ガス(アルゴンガスや窒素ガス)を高圧で噴射することによって製粉する方法で、工業的に最も利用されている製粉プロセス。その他、水アトマイズ法、ディスクアトマイズ法、プラズマアトマイズ法、プラズマ回転電極法などがある。 |
3 | チタン | チタンには、純チタンとチタン合金がある。純チタンは、1種、2種などがあるが、1種のほうが純度が高く、柔らかい。チタン合金は、Ti–6Al–4V 合金(Ti64とも呼ばれる)がよく用いられる。チタンは比強度および耐食性、耐熱性に優れるが、摩耗に弱い。比重は鉄とアルミの中間で軽い金属であるにもかかわらず、強度が高い。特にチタン合金は、最大クラスの比強度をもっている。粉末状の材料として、PBF, DED, BJTで用いられる。耐熱性や強度の高さを活かして、航空機、潜水艦、自転車、ゴルフクラブの材料として使用される。また、生体適合性が高いので、医科用・歯科用のインプラントとしても用いられる。 |
4 | インコネル | インコネルはニッケルを主体とした合金であり、インコネル625合金、インコネル718合金などがある。625は広範囲の腐食環境での耐性に優れ、718は低温から高温まで幅広い温度下での強度や耐食性に優れている。インコネルは、機械特性、溶接性、耐食性、対酸化性、高温下や高圧下での高い耐久性に優れる。粉末材料として、PBF, DED, BJT、ワイヤー材料としてDED(WireARC)、フィラメント材料としてMEXで使われる。航空宇宙、エネルギー、海洋、プラント用途に広く用いられる。 |
5 | ステンレス | ステンレスはクロムや炭素を含む錆びにくい合金であり、代表的なものとしてSUS316L、17-4PHなどがある。SUS316Lは耐食性、靭性、延性に優れ、さらに酸に対する高い耐性がある。航空宇宙、自動車、エネルギー、宝飾品、医療、造船などに用いられる。17-4PHは高強度と高レベルの耐食性を備えており、手術器具などの医療用途に適している。粉末材料として、PBF, DED, BJT、ワイヤー材料としてDED(WireARC)、フィラメント材料としてMEXで使われる。 |
6 | ツール鋼 | ツール鋼は工具や治具向けの材料である。代表的なものとしてマレージング鋼、ツール鋼1.2709などがある。マレージング鋼は機械的特性、硬度、強度に優れ、射出成型、機械部品に用いられる。ツール鋼1.2709は機械的特性、疲労強度に優れ、用途に応じた硬度と強度を熱処理で得ることができる。射出成型、押出ツール、ホットプレスなどに用いられる。粉末材料としてPBF, DEDで、フィラメント材料としてMEXでも用いられる。 |
7 | 銅 | 鋼は純銅と銅合金に分類される。純銅は高純度の銅であり、優れた導電性と熱伝導性をもつ。熱交換器やエレクトロクスで用いられる。銅合金の代表的なものとしてCuCrZr 合金があり、良好な機械的特性に加え、導電性と熱伝導性も兼ね備えている。ロケットエンジン部品や熱交換器、誘導コイルなどに用いられる。従来、純銅は高い反射率を持つため、レーザーPBFでは造形が難しかったが、近年、グリーンレーザーの採用によりPBFでも造形が可能になっている。同じく粉末材料として、BJT、EBMでも造形が可能である。また、フィラメント状の材料として、MEXでも用いられる。 |
8 | アルミニウム | AMでよく用いられるアルミニウムは合金である。代表的なものとして、AlSi10Mgがあり、強度、硬度、耐食性、熱伝導性、電導性、軽量性に優れる。軽量設計が必要な部品、航空宇宙、自動車などに用いられる。粉末材料としてPBF、BJTで造形が可能である。 |
9 | コバルト基合金(CoCrMo) | コバルトやクロムなどのレアメタルによる合金である。機械的特性、耐食性、高温下の特性に優れる。ニッケルフリーであり、微細で均一な結晶粒構造を示す。航空宇宙、医療などで用いられる。粉末材料としてPBF、BJTなどで用いられる。 |
⑤その他材料
No. | その他 材料 | 説明 |
1 | 石膏 | 硫酸カルシウムが主成分の無機物。BJT方式の造形に用いられる。造形物はもろくてあまり強度がないため力が加わるものには不向きであるが、着色することができるのでフィギュアの原型や模型製作などに用いられることが多い。 |
2 | セラミックス | 金属や樹脂と異なり共有結合を主として構成される無機物質のことを指す。広義では砂や石膏、ガラスを含み、狭義では高純度のファインセラミックスを指す。3Dプリンターでは材料として両方用いるが、本項では後者について説明する。セラミックスは、大きく分けて酸化物系と非酸化物系に分けられる。酸化物系の代表的なものにアルミナやジルコニアがある。アルミナの特徴は高強度、高融点、耐摩耗性、高電気抵抗、高硬度、化学安定性であり、電気・電子領域や実験器具、光学部品に用いられている。ジルコニアの特徴は、高強度、高硬度、化学安定性、審美性、断熱性であり、消費財や医学装置、インプラント、電子装置、燃料電池などに用いられている。非酸化物系の代表的なものは窒化ケイ素である。窒化ケイ素の特徴は高硬度、耐熱衝撃、耐摩耗性、耐腐食性であり、バルブ部品やエレクトロクスポンプなどで用いられている。セラミックスは、粉末材料としてPBF, BJで、フィラメントやペレット材料としてMEXで、ペースト状・スラリー状の材料にしてMJTやVPPで用いられている。造形によって成形した後、焼結工程を通して熱を与えて緻密化する。焼結工程では10%~20%収縮する。焼結後の部品は高い硬度を有するため、切削加工などで形状を整えることが困難になる。ゆえに高精度な複雑形状の作製が課題である。 |